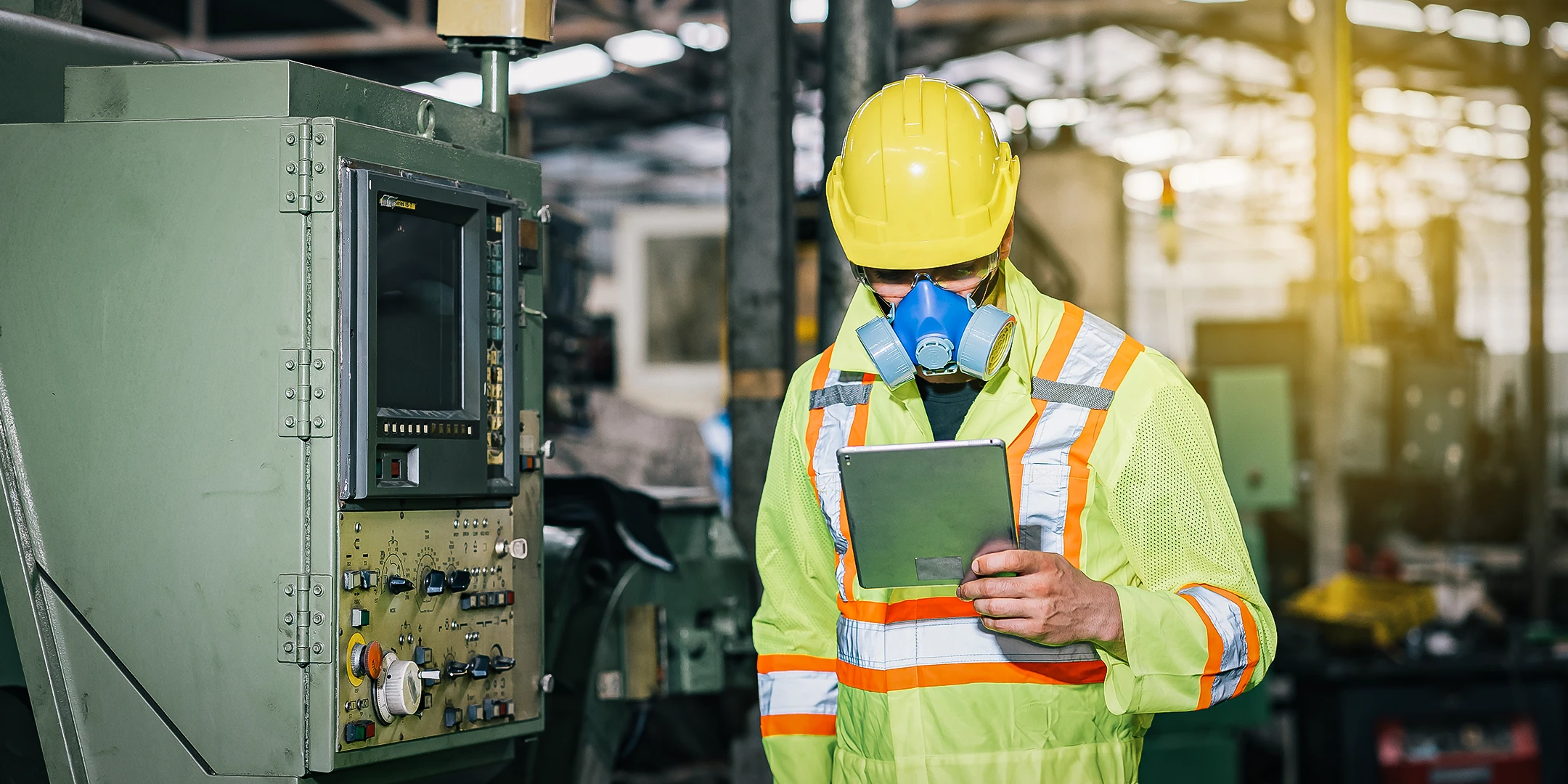
PPE training: digital and efficient
Did you know that wearing suitable eye protection can avoid around 90 per cent of eye injuries in everyday work? This is just one example of how necessary personal protective equipment (PPE) is. However, correct use can only be achieved if all employees know how to wear, care for, and check the PPE. Therefore, detailed PPE trainingis a top priority before employees wear protective clothing.
When providing instruction on personal protective equipment, there are a few special features to consider. We will explain the applicable requirements and give you tips on how to do the associated exercises successfully. Electronic instructions, for example, provide support for this. You can find out how to use a software solution for this purpose in our free ebook!
The big book of digital HSQE management
Find out in detail how a comprehensive software solution can support you in the area of HSQE!
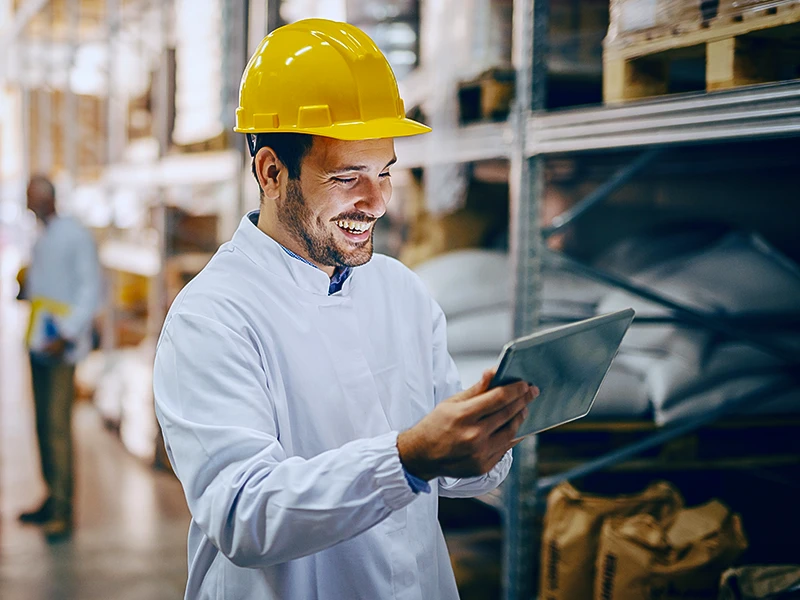
Personal protective equipment: Why do you have to train your employees?
Why is PPE training necessary – isn’t protective equipment self-explanatory after all? A simple answer to this question is that law requires personal protective equipment training in many countries. However, the reasons for this go much further because it is not uncommon for PPE to be used incorrectly or left out completely. It is, therefore, crucial to show your employees the consequences of improperly used or damaged protective equipment. Work accidents are becoming more common, particularly when employees believe they are protected, but there is inadequate protection against hazards.
Also, keep in mind that the use of personal protective equipment places an additional burden on many employees. To make it easier for employees to use PPE and to motivate them to use it regularly, they must know how to use it safely. Employee training is an essential success factor for this. There are, therefore, more than enough arguments for regularly practicing the correct use of PPE.
It is crucial not only to inform employees about use, care and storage. Checking the PPE before each use is also an important part of the instruction. Only with a visual and functional inspection for defects, wear or material fatigue can employees forestall potential dangers.
Personal protective equipment in short:
In principle, PPE is only used when technical or organizational measures to protect against dangers in the workplace are no longer sufficient. Examples are protective gloves, safety glasses, safety helmets or safety shoes. If these are necessary, the employer must make them available to employees free of charge and ensure that they are in proper condition. PPE can be divided into three risk categories. It is important that the PPE has a CE marking. Which PPE is suitable is determined in the hazard assessment. The obligation for employees to wear clothing is also stated in the respective operating instructions.
What legal requirements are there for PPE instruction?
Regulation (EU) 2016/425 is primarily aimed at PPE manufacturers. It was published in 2016, replacing the PPE directive 89/686/EEC. The PPE directive aims to ensure a uniform European level of safety. Therefore, among other things, three PPE categories are defined, and guidelines are given as to which PPE the employer must provide training for. Also included are specifications for the declaration of conformity.
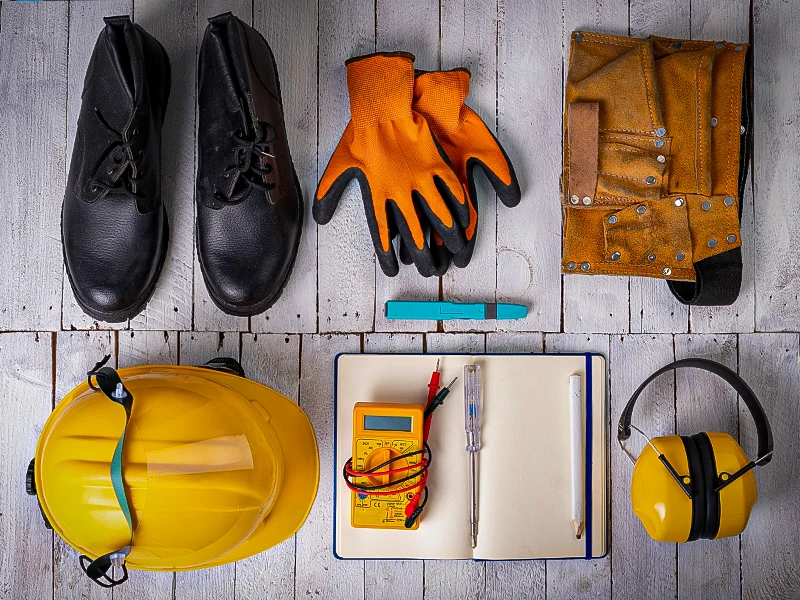
- Category 1: Protection against minor hazards – e.g. protective gloves
- Category 2: Protection against medium risks – e.g. helmet or safety glasses
- Category 3: Protection against permanent damage to health or fatal risks – e.g. respirators, hearing protection, PPE against falls
Below, we will answer some common questions regarding PPE. Please be aware that these regulations might differ in your country.
Who provides training on PPE?
The employer generally bears overall responsibility. However, this person can also commission other people to provide safety instructions. As a rule, having a direct supervisor in the relevant area of responsibility makes sense, but occupational safety specialists, company doctors, and other safety officers can also be considered.
The person responsible must have specialist knowledge and experience in handling the PPE. They should also be able to demonstrate practical exercises, correct use, and recognize typical usage errors.
Who do you need to train?
Of course, you must provide appropriate training to all employees who use PPE. Remember that this also applies to trainees, temporary workers, temporary employees and freelancers. You must document every PPE training session and have all participants sign it.
When and how often is PPE training required?
A simple basic rule is:
Employees’ initial training must occur before using PPE. In addition, you should repeat the training regularly, preferably once a year. For young employees, PPE training is even required/recommended every six months.
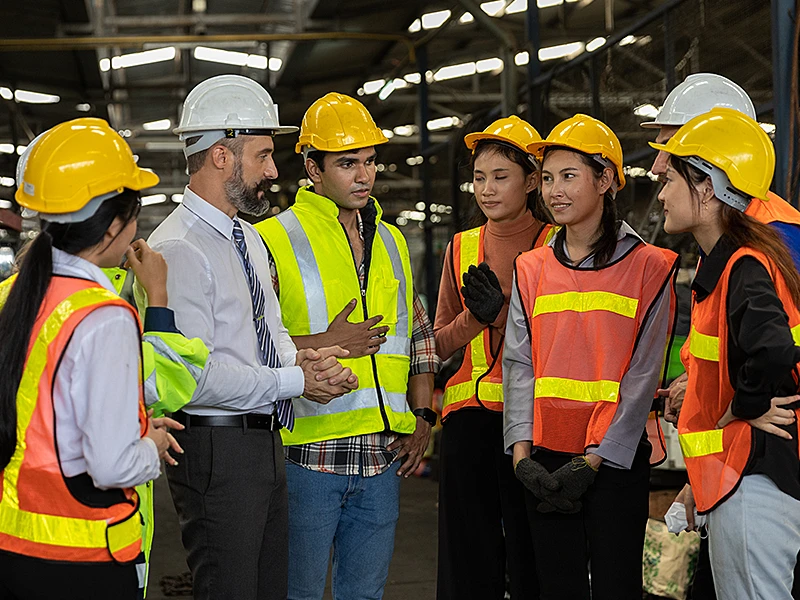
Other occasions that make instruction necessary include (selection):
What content should you include in the PPE training?
In addition to the intended use, the limits of use, the duration of wear and the storage and care of the PPE, you should also consider the following topics in your training (selection):
Explain to your employees the importance of PPE in occupational safety and how employees can correctly put on and take off protective equipment. Another common question is how workplaces are marked where PPE is required. A short knowledge test rounds off your training and shows any gaps in understanding.
What are the special features of PPE training?
In principle, PPE training without practice is sufficient in most cases. However, there are exceptions: for example, in German law, special training is required for protective equipment that is intended to protect against fatal risks or permanent damage to health. In concrete terms, this must be implemented with practical exercises.
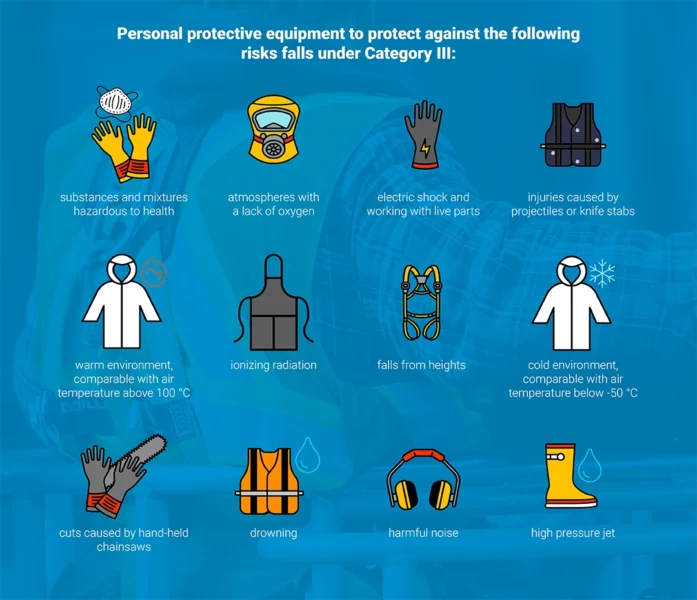
The exercise aims to ensure that your employees can use the PPE safely in their work tasks and behave correctly in critical situations. Practical training is an essential requirement so that employees not only know how to protect themselves from life-threatening dangers or irreversible damage to their health in theory. After all, a lot can go wrong, even when inserting a simple ear plug. To this end, conveying the manufacturer’s information on the respective PPE in the training with practice is a good idea.
Tips for PPE instruction with practice
You should carry out special training with exercises before using the PPE for the first time. Practical instructions are also not exempt from regular refreshers, due at least once a year. It is important that you always carry out the exercises under comparable working and operational conditions and tailored to the respective area of activity.
Also, carry out the exercises in appropriate group sizes. We recommend that you instruct no more than six people at once, so that the exercises can take place with sufficient time for repetitions and feedback. Your employees will become more experienced in using the PPE, and you will notice application errors more quickly.
How can PPE training be carried out digitally?
PPE that does not require training and practice can be easily implemented using a digital tool. However, for special training that requires practice, more than online training isneeded to familiarise your employees with the PPE. It makes sense to add exercises for use in the workplace and to specifically address the hazardous situation in your company.
However, providing basic manufacturer information on PPE in the theoretical part of training courses digitally is still advisable. If theelectronic training meets the following criteria, it can also be used for the subject of PPE:
- The training content must be tailored to the work area.
- The understanding of the employees is checked.
- The opportunity for feedback and questions must be guaranteed.
- Legally compliant documentation is provided.
Our software solution iManSys meets all of the requirements mentioned: You can enter individual instructions and assign them directly to employees who require PPE. You can then check the learning success of your employees in integrated comprehension tests. You will automatically receive a legally compliant certificate of instruction upon completion.
It is particularly effective if you first impart the basic theoretical knowledge of PPE using an instruction software and then carry out the practical on-site exercises. We recommend the integrated event planning in iManSys. This means you can prepare and implement your PPE instruction with minimal effort and maximum success. You can find out more information about the use of electronic instruction in our associated ebook. We hope you enjoy reading!
The big book of digital HSQE management
Find out in detail how a comprehensive software solution can support you in the area of HSQE!
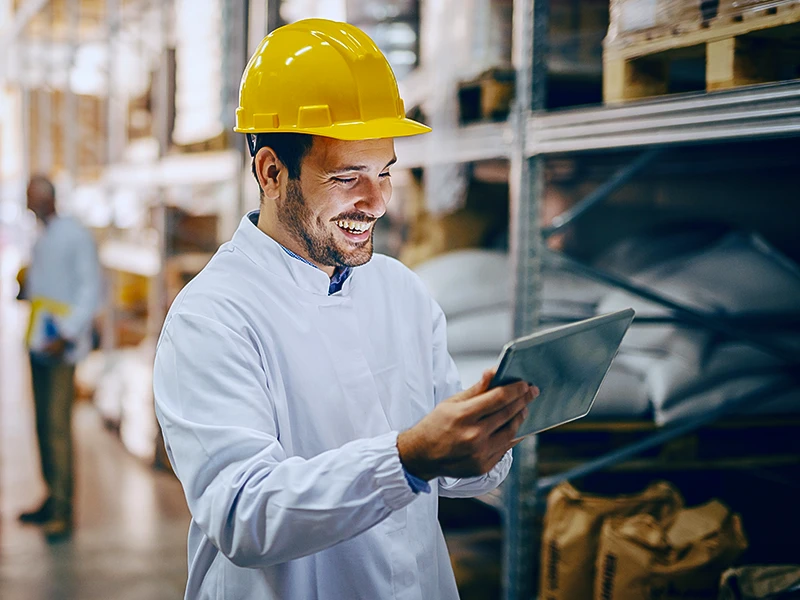
Share this article:
More blog posts
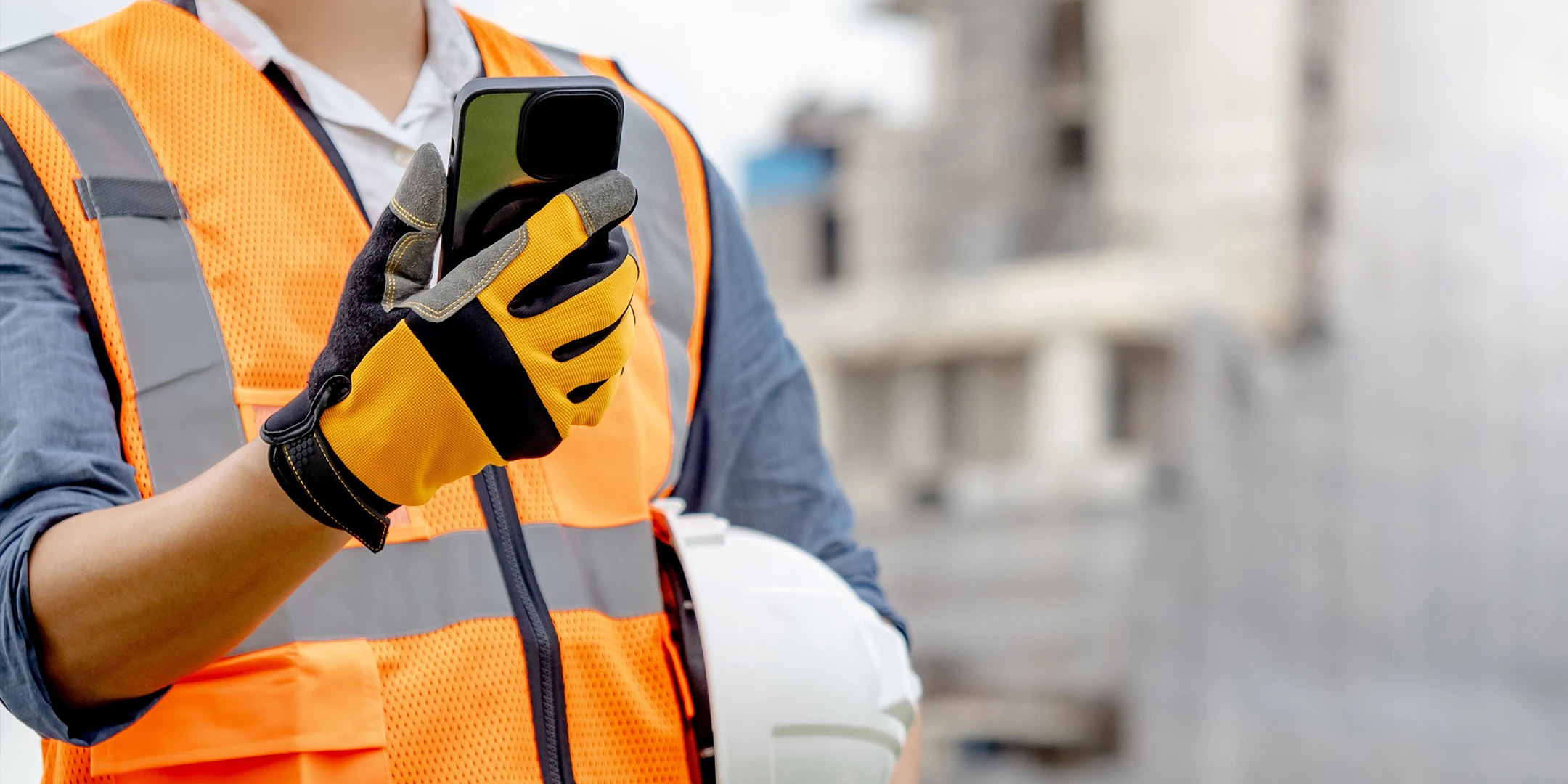
Mobile Occupational Safety
What’s the first thing that comes to mind when you hear the term “occupational safety” ? Perhaps personal protective equipment, specifically a hard hat. Or risk assessments, training, company guidelines. […]
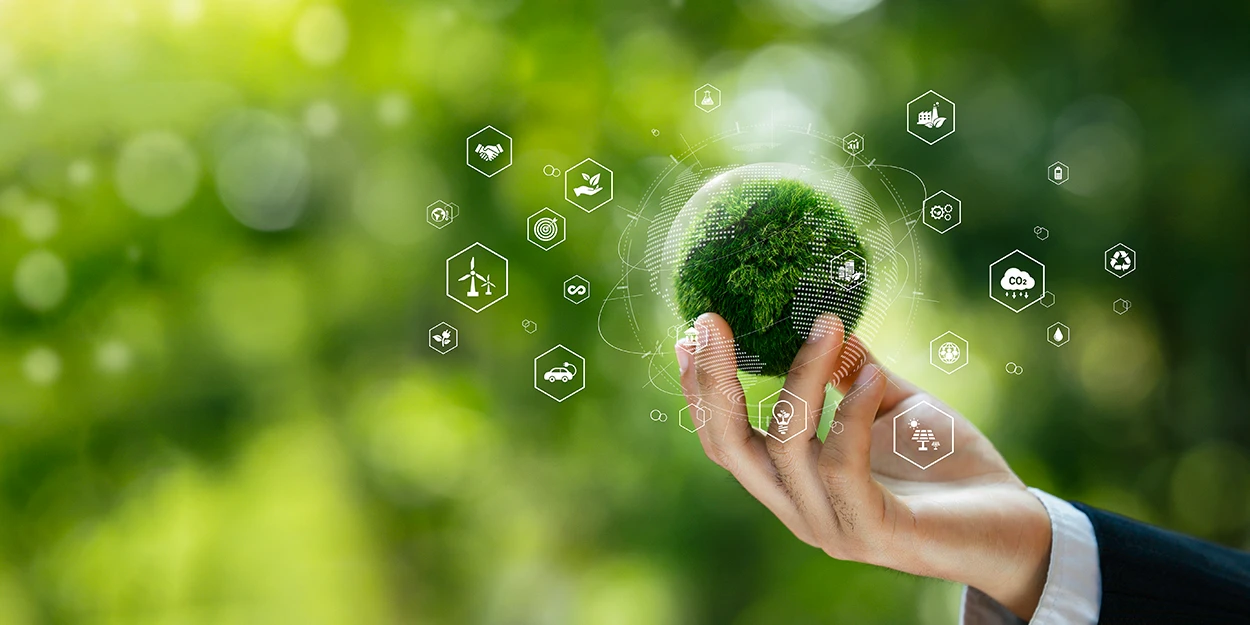
The key to sustainable success
Companies throughout Germany must gradually deal more intensively with the three letters ESG: Environmental Social Governance. Pursuing sustainability goals not only has a positive impact on the environment but is […]
Leave a Reply